JIATONG XJ is One of China's Professional Sheet Metal Manufacturer and Fabricator Since 2011 in Dong Guan City, Which Offers One-stop Wholeset of Sophisticated Production Solutions for Customers Globally. Main Market: US. Europe, Southeast Asia.etc Machining Scope:Precision Laser Cutting, Fiber Laser Cutting, CNC Robot Bending, Riveting, Welding, Broaching, Drilling, Tapping, CNC Machining, Metal Finishing, Assembling etc. Alu Bracket

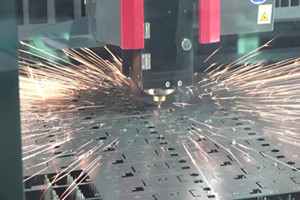
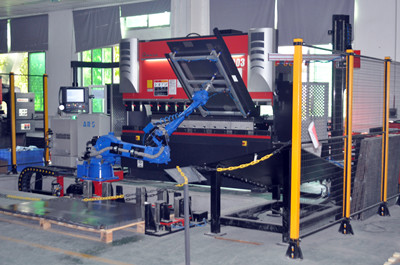
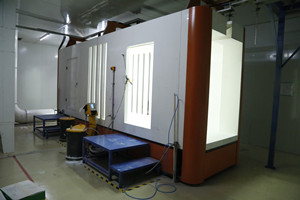
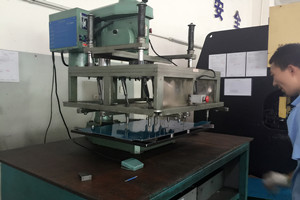
Other Processes:Drilling/Tapping/Welding/Powder Coating/Assembling.
What are the common surface treatment methods for sheet metal processing? Several common surface treatment methods for sheet metal processing are: wire drawing, sandblasting, baking paint, powder spraying, electroplating, anodizing, and silk screen printing. Since the surface of some sheet metal materials does not have the ability to prevent rust and corrosion, it is very necessary to carry out effective surface treatment. Surface treatment of sheet metal parts can improve product life in harsh environments, or to achieve specific surface effects or functions. Among the sheet metal processing materials, cold-rolled sheets and hot-rolled sheets are relatively less resistant to corrosion, and are prone to oxidation reactions and continue to deepen corrosion. Cause sheet metal parts to lose performance or be scrapped. Therefore, it is necessary to achieve the purpose of anti-corrosion and rust prevention through surface treatment. What are the surface processes of sheet metal processing?
Introduction to the surface treatment process of sheet metal parts:
-
Brushed The so-called sheet metal drawing is to place the material between the upper and lower wheels of the wire drawing machine, and the wheel is attached with an abrasive belt, which is driven by a motor to let the material pass through the upper and lower abrasive belts, and pull out traces on the surface of the material. Different, the thickness of the traces is not the same, the main role is to beautify the appearance. In addition, drawing is also called rubbing! Common materials for this surface treatment process: generally aluminum and stainless steel sheets are considered to be brushed surface treatment methods.
-
Sandblasting The sand is hit on the surface of the workpiece by the wind of the sandblasting machine, forming a dense layer of pits on the surface of the workpiece. Prepare. Common materials for this surface treatment process: cold-rolled sheet, hot-rolled sheet, aluminum, etc.
-
Spray paint It generally refers to liquid spraying. There are two kinds of processes: liquid baking paint and self-drying spray paint. Self-drying means that after spraying, it can be cured naturally at room temperature. The cost is low, but the effect is incomparable to baking paint. The color effect of spray paint will be better, and the thickness of the paint film is relatively thin, which is suitable for some precision products, and the cost is higher. Common materials for this surface treatment process: cold-rolled sheet, hot-rolled sheet, etc. Sheet metal processing surface treatment painting process A.The base layer of sheet metal processing products should be derusted first. Such as: sandblasting, phosphating, etc. B.Sheet metal processing products are used as epoxy zinc-rich primers, which are mainly used for anti-rust primers for steel structures and steel products. The coating film has good physical and chemical properties, easy construction and good matching performance. The main components are: ring Oxygen resin, epoxy curing agent, zinc powder, anti-rust pigment, auxiliary agent and organic solvent, etc. C.Sheet metal processing products as epoxy micaceous iron intermediate paint: used in conjunction with epoxy zinc-rich primer, as a long-term anti-corrosion coating transition layer, its role is to enhance the sealing and anti-corrosion of the composite coating, and can also be used As an anti-corrosion and anti-rust primer. The coating film is strong and tough, with good adhesion and sealing, and is well matched with the front and rear coatings. Its components are: epoxy resin and curing agent, iron oxide and anti-rust pigment, etc. D.Sheet metal processing products as the surface layer. Its surface layer can be used for epoxy asphalt topcoat, chlorinated rubber topcoat, acrylic and polyurethane topcoat, fluorocarbon topcoat, etc.
-
Plastic spraying (also called powder spraying) It means that the powder is polarized and evenly attached to the surface of the product with the opposite polarity under the action of the electric field force. Features of spray plastic: wear resistance and corrosion resistance are relatively good, the film is relatively thick, suitable for relatively thick products such as cabinets and equipment, the cost is low, and the plastic powder can be recycled. Common materials for this surface treatment process: cold-rolled sheet, hot-rolled sheet, etc. Electrostatic powder spraying mainly polarizes the paint (powder) through the electrode, and then charges the object to be sprayed with the opposite charge, and the powder evenly adheres to the surface of the object under the action of the electric field force.
-
Electroplating Through chemical reaction, a layer of other metal is attached to the surface of the material, which is used to increase the corrosion resistance of the metal, and can achieve a certain effect of beautifying the appearance. It is a commonly used surface treatment method. Such as: electroplating zinc, electroplating nickel and so on. Mainly plated with colorful zinc, blue and white zinc, black zinc and chrome plating. Common materials for this surface treatment process: cold-rolled sheet, hot-rolled sheet, etc. Sheet metal processing surface treatment electroplating process: Types of electroplating: a.Galvanizing:1.Cyanide galvanizing 2.Zinc galvanizing 3.Chloride galvanizing 4.Sulfate galvanizing. b. Chrome plating c.Gold plating d.Copper plating e.Nickel plating f.Other metal plating
-
Anodizing Oxidize the metal on the surface of the workpiece to form a dense protective film on the surface of the workpiece to increase the corrosion resistance of the workpiece. Generally, there are two ways of chemical oxidation and anodic oxidation. It is a common surface treatment method, usually with primary color anodizing and black anodizing. Common material for this surface treatment process: aluminum.
-
Silkscreen The process of silk-screening various logos on the surface of the material generally has two methods: flat screen printing and pad printing. The main principle is the same as that of camera film imaging, and it is also a process of exposure. Flat screen printing is mainly used on general planes, but if you encounter Where there are deep pits, pad printing is required. Usually used in trademarks, usage signs, warning signs, etc.
-
Phosphating Phosphating is a commonly used pretreatment technology, and in principle it should belong to chemical conversion film treatment. It is mainly used for phosphating on steel surfaces, and non-ferrous metals (such as aluminum and zinc) can also be phosphating.The main purpose of phosphating is to provide protection for the base metal and prevent the metal from being corroded to a certain extent; it is used as a primer before painting to improve the adhesion and anti-corrosion ability of the paint film; it is used to reduce friction in the metal cold working process. Lubrication. Common materials for this surface treatment process: cold-rolled sheet, hot-rolled sheet
-
Dip The product is heated in the molten material, and the heated metal combines with the surrounding molten material to form a surface material of a certain thickness. According to the different raw materials used in dipping, it can be divided into liquid dipping (coating) molding and powder dipping (coating) molding. Such as: our daily clothes hangers, pliers, rubber sleeves on scissors, water valve wrenches, etc. Common materials for this surface treatment process: cold-rolled sheet, hot-rolled sheet. CNC sheet metal fabrication surface treatment dipping process Metal dipping is a new type of technical treatment process for metal surface anticorrosion. Dipping is a heating process, metal preheating, dipping, and curing. During dipping, the heated metal sticks to the surrounding material. The hotter the metal, the longer the dipping time and the thicker the material.
-
Commonly used stainless steel surface treatment process Wire drawing, polishing: According to the complexity of stainless steel products and different user requirements, mechanical polishing, chemical polishing, electrochemical polishing and other methods can be used to achieve mirror gloss. Sandblasting, scratching, whitening treatment: During the processing of stainless steel, black oxide skin is produced by rolling, edging, welding or artificial surface fire heating treatment. This hard gray-black oxide scale is mainly composed of two EO4 components, NiCr2O4 and NiF. In the past, hydrofluoric acid and nitric acid were generally used for strong corrosion removal. However, this method has high cost, pollutes the environment, is harmful to human body, and is highly corrosive, and is gradually eliminated.
-
At present, there are two main methods of oxide skin treatment:(1) Sand blasting (pellet) method: mainly use the method of spraying micro glass beads to remove the black oxide scale on the surface. (2) Chemical method: use a non-polluting pickling passivation paste and a non-toxic cleaning solution with inorganic additives at room temperature for dipping. So as to achieve the purpose of whitening the natural color of stainless steel. After processing, it basically looks like a dull color. This method is more suitable for large, complex products.
-
Coloring methods:(1) chemical oxidation coloring method; (2) electrochemical oxidation coloring method; (3) ion deposition oxide coloring method; (4) high temperature oxidation coloring method; (5) gas phase cracking coloring method. Other surface treatment methods such as baking paint, enamel, etc. are not commonly used for chassis and cabinet sheet metal processing products.
-
Passing Certification ISO9001 2015 Quality Control and Inspection Facilities and Methods:Two-dimension detector, Projector, Height gauge, Paint adhesion detector, Paint color difference detection, Paint thickness test, Angle test, Thread gauge, Microcalliper Gauge.etc Inquire immediately
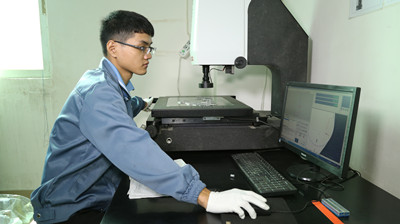
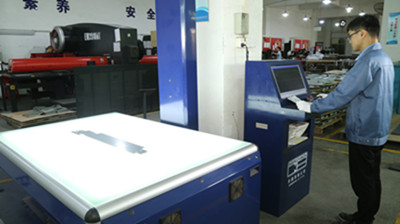
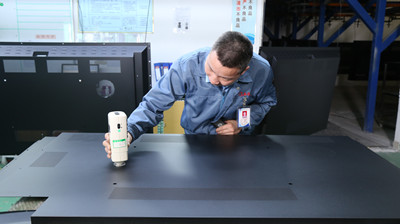
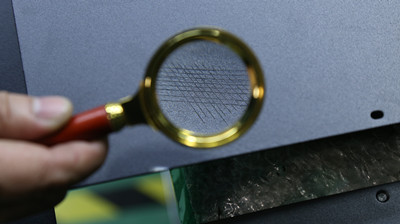
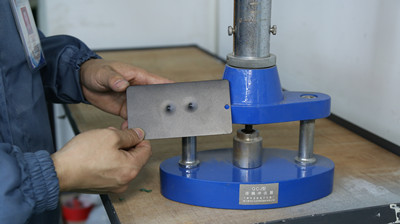
Industries:Electronic Devices, Smart Terminal, Industrial Equipment, Mechanical Sheet Metal Parts, Equipment Cabinet, Display Screen Bracket, Telecommunication Parts, Construction, Marine Industry, New Energy, Garden Lawn Mower Parts, Military Industry, Bank Financial hardware parts,auto components, Computer electronics, Electronics components, Civil Engineering,Construction,Marine Industry,Garden Products, Military industry.etc click here to learn more details.
Packaging:Plywood Carton and Pallet, Independent box, Bubble or Foam, Polybag. Port: Shenzhen or Guangzhou.
QUICK LINKS: FAQ / EQUIPMENT LIST / MATERIAL / CUSTOM SHEET METAL / SHEET METAL SUPPLIER / SHEET METAL ENCLOSURE / SHEET METAL COVER / METAL CHASSIS / SHEET METAL CHASSIS / MOUNTING BRACKET | Alu Bracket